Crafting the Katana: An In-Depth Journey from Raw Steel to Masterpiece.
- battlingblades643
- Nov 30, 2023
- 3 min read
The traditional crafting of a katana sword is a meticulous process deeply rooted in Japanese history and craftsmanship. From selecting raw materials to the final polishing, each step contributes to the creation of a sword that embodies both functionality and artistry. Let's delve into the intricate process of making a traditional katana from start to finish.

1. Raw Materials Selection:
The foundation of every katana lies in the selection of raw materials, with Tamahagane steel being the primary choice. Tamahagane is produced through a labor-intensive smelting process, utilizing iron sand in a Tatara furnace. This furnace, fueled by charcoal, refines the iron sand into high-carbon steel, characterized by its unique grain patterns.
2. Smelting and Refining:
The smelting process is a delicate dance of temperature and time. Skilled craftsmen layer different grades of Tamahagane to achieve the desired properties in the final blade. The layered steel is then carefully shaped into a rectangular billet, setting the stage for the forging process.
3. Forging the Blade:
The forging of the blade is a meticulous art form that requires both precision and experience. The rectangular billet is heated and hammered repeatedly to shape the blade, elongating it and giving it a curvature known as "sori." The repeated folding and hammering contribute to the distinctive grain pattern in the steel, enhancing both its strength and aesthetic appeal.

4. Differential Heat Treatment:
A critical step in katana crafting is the differential heat treatment. The blade is covered in a special clay mixture, leaving the edge exposed. When heated and quenched, the clay-coated portion cools more slowly than the exposed edge, creating the signature Hamon line. This process not only defines the sharpness of the blade but also adds an artistic element.
5. Shaping the Tang and Hilt Components:
As the blade takes shape, attention turns to the tang, or "nakago," which extends from the blade into the hilt. The tang is shaped and prepared for the hilt components. Craftsmen meticulously carve the hilt from wood, creating a comfortable grip. Rayskin or leather is then applied for additional texture and durability.
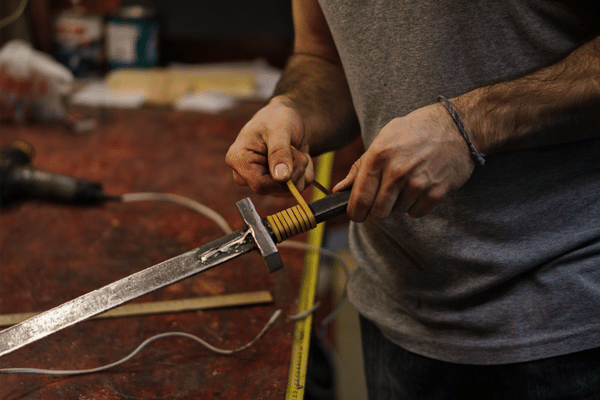
6. Hilt Assembly:
With the tang prepared and the hilt components in place, the Swords begin to take their final form. The hilt is carefully wrapped with silk or cotton cord in a traditional pattern known as "ito." The guard, or "tsuba," is fitted onto the tang, serving both functional and ornamental purposes.
7. Ornamentation and Personalization:
Katana makers often add decorative elements to personalize the sword. Menuki, small ornaments, are placed beneath the hilt wrap, adding both aesthetic value and a tactile reference point. Fuchi-kashira, the pommel, and collar are also added, often featuring intricate designs or symbolic motifs.

8. Polishing:
Once the sword is fully assembled, it undergoes an extensive polishing process. This step is crucial for revealing the true beauty of the blade and removing any imperfections from the forging and assembly stages. The polishing is done by skilled artisans who use various grades of stones to achieve a razor-sharp edge and a flawless finish.
9. Quality Inspection:
Before a katana is considered complete, it undergoes a rigorous quality inspection. Craftsmen examine every detail, ensuring that the blade is symmetrical, the fittings are secure, and the overall craftsmanship meets the highest standards. Any deviations are addressed before the final steps.
10. Final Touches and Signatures:
The last steps involve adding the final touches, such as a protective lacquer coating and the artisan's signature on the tang. The signature not only authenticates the sword but also serves as a mark of pride for the craftsman, linking their name to a tradition that spans centuries.
Conclusion:
Crafting a traditional katana is a journey that requires a blend of ancient techniques, artistic sensibility, and a deep understanding of metallurgy. From the selection of raw materials to the final strokes of the polishing stone, each step contributes to the creation of a masterpiece that embodies the spirit of Japanese craftsmanship. The traditional katana, with its rich history and intricate crafting process, stands as a testament to the enduring legacy of the samurai and the artistry of swordsmiths throughout the ages.
Opmerkingen